This study develops a ferrofluid-lubricated thrust bearing with an air cushion. The bearing comprises a rotor, a stator, and a ferrofluid ring formed between them due to absorption by an annular magnet under the stator. The design makes it possible for the air cushion (air sealed inside the ferrofluid ring) as well as the magnetized ferrofluid to supply supporting forces. A model of the bearing for a static supporting force is proposed and validated by experiments. As the gap between the rotor and stator was 0.25 mm, the maximum static supporting force of the bearing was 3.2 N, much higher than the support provided by the pure ferrofluid ring (without the air cushion, 1.7 N). The operating space of the bearing was detected by multicycle load–retract tests with remarkably high and repeatable accuracy. The results of dynamic experiments show that the speed of rotation of the rotor has a minor effect on the supporting force. Such a ferrofluid-lubricated bearing offers promise for use in precise positioning or low-friction systems.
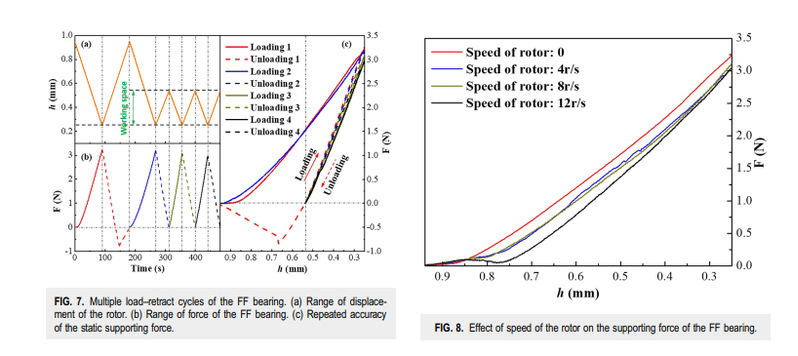
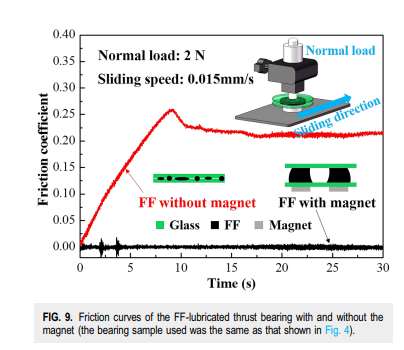
全文下载:
Ferrofluid-lubricated thrust bearing with an air cushion.pdf